Vacuum decay leak detection is a non-destructive method used to verify the integrity of sealed packaging. The core principle involves detecting pressure changes in a vacuum environment to identify potential leaks.
Process Overview
- Vacuum creation: The test sample is placed in a sealed chamber, which is then evacuated to a specific vacuum level (e.g., absolute pressure of 50–100 kPa).
A leak-free sample will maintain equilibrium with the vacuum chamber, whereas a leaking sample will allow external air to infiltrate through the defect. - Pressure monitoring: Once the vacuum stabilizes, the vacuum pump is isolated, and a high-precision sensor monitors pressure changes within the chamber.
- No leak: Pressure remains stable.
Leak present: Air enters the chamber, causing the pressure to rise (i.e., vacuum level decreases).
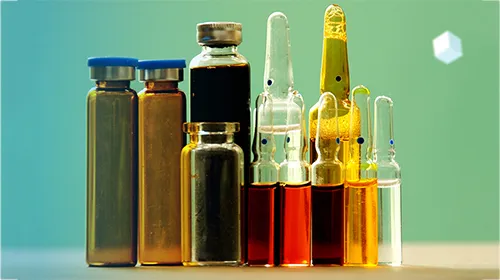
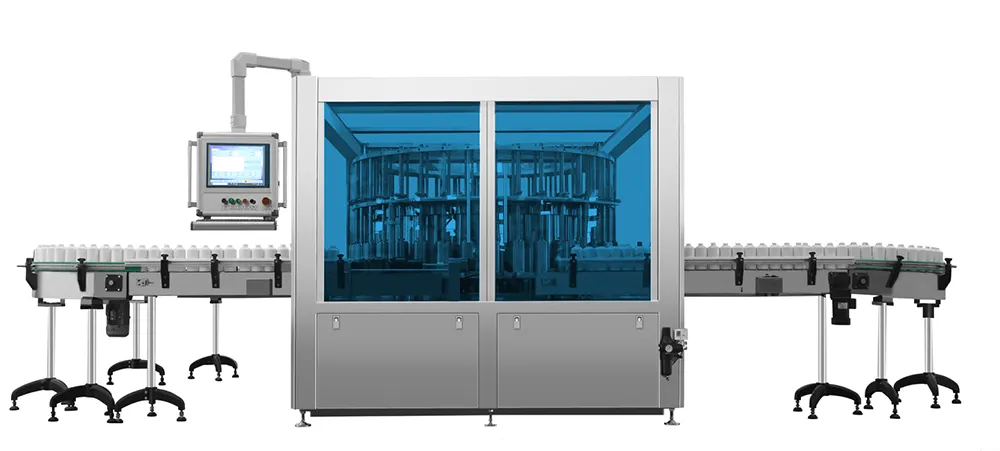
Advantages
- Non-destructive testing: Detects leaks without opening or damaging the package, allowing the sample to remain usable or saleable after inspection, reducing waste.
- High sensitivity: Capable of detecting extremely small leaks (typically down to 1–5 microns in diameter), ideal for high-value, sterile products and vacuum-sealed items.
- Fast and efficient: Short inspection times make it suitable for in-line testing on production lines, improving productivity.
- Wide applicability: Compatible with various packaging formats (e.g., flexible pouches, rigid containers, blister packs) and materials (e.g., plastic, glass, metal), regardless of shape.
- Quantitative analysis: Pressure variations can be used to quantify the leak size, providing concrete data for quality evaluation and traceability.
- Environmentally friendly and safe: No need for water, chemicals, or other mediums (unlike the water bath method), minimizing contamination risk and aligning with green manufacturing standards.
- Automation compatibility: Easily integrated into automated production lines for fully automated inspection, reducing human intervention and increasing consistency and reliability.
- Cost-effective: Low long-term maintenance costs and reduced product loss due to non-destructive testing make it more economical than traditional destructive methods.
- Industry standard compliance: Recognized by international standards such as ASTM F2338 and ISO 11607, meeting regulatory requirements in pharmaceutical, food, and other industries.
- No contamination risk: Eliminates the moisture or secondary contamination risks associated with water bath testing, especially suitable for sterile or moisture-sensitive products.